Le montage semble simple, néanmoins, afin d'obtenir quelque chose faisable en (petite) série, cela a quand même demandé beaucoup de temps au final quand on met tout bout-à-bout, et comme j'ai pris pas mal de photo pour les tenir au courant de l'avancement du projet, j'en fais une petite page pour en faire un récapitulatif.
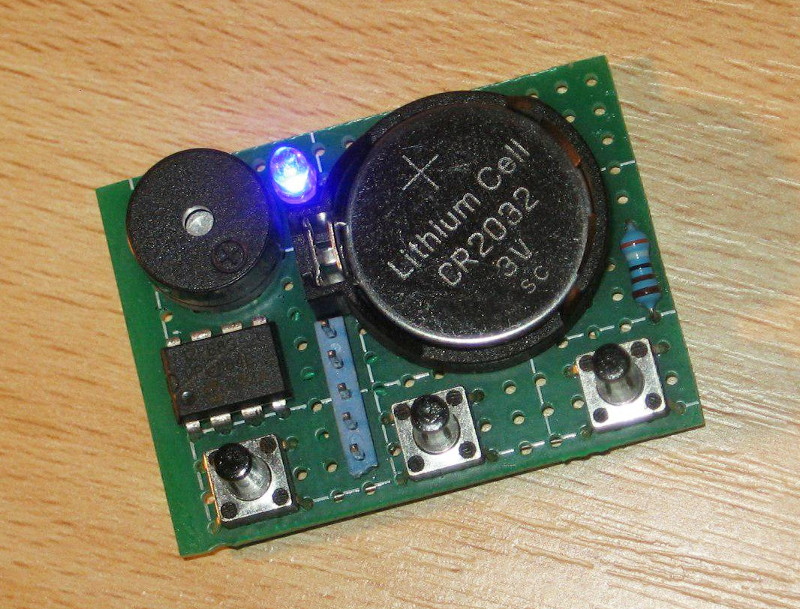
Le prototype du timer réalisé sur plaquette à trous
- Bouton 1 : Lance un minutage de 15 secondes, la led flashe rapidement pendant cette durée
- Bouton 2 : Lance un minutage de 30 secondes, la led flashe moins rapidement pendant cette durée
- Bouton 3 : Lance un minutage de 45 secondes, la led flashe lentement pendant cette durée
- Maintenir le bouton 2 puis appuyer sur le bouton 1 ou 3 permet de diminuer ou d'augmenter la hauteur du son émis par le buzzer en fin de minutage
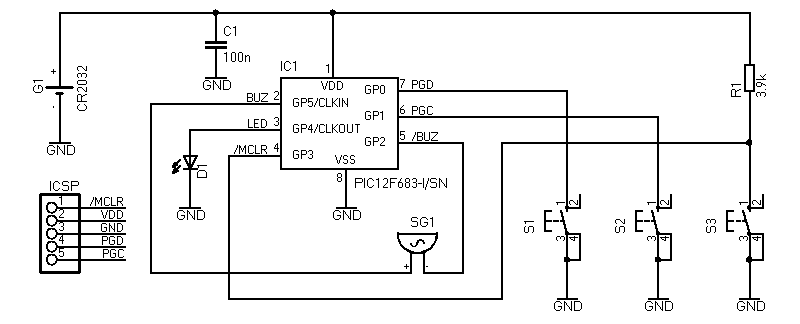
Un schéma tout con. Un bouton pour chaque durée, une led, et un buzzer.
Le réglage de la fréquence sonore est important car ces buzzers n'ont pas du tout une courbe de réponse en fréquence plate, et ça permet de trouver une fréquence de résonnance où le volume est plus fort. Pour avoir un volume maximal malgré la tension limitée de la pile, les deux côtés du buzzer sont commandés en opposition de phase, afin de doubler la tension crête-à-crête aux bornes du buzzer. En pratique, ça sera le buzzer lui même qui limitera le volume sonore... Concernant le firmware, en voici le code source ainsi que le fichier .hex pour le flash du 12F683. Toutes les pattes du µC sont utilisées (même /MCLR, qui n'a pas de "weak pull-up" intégré quand il est en mode I/O et il lui faut donc une résistance externe. Et apparemment il faut faire attention quand on écrit le firmware de ne pas tout de suite toucher aux lignes PGC et PGD sinon on ne pourra pas le reflasher vu qu'il n'y aura plus la broche de reset).
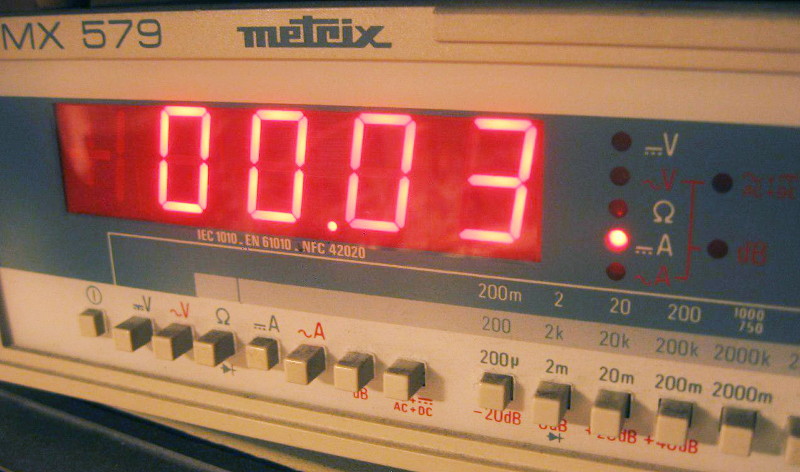
Mesure du courant consommé en veille
Mon multimètre le plus sensible mesure une consommation de courant en veille de 30nA. Une CR2032 de 200mAh devrait donc pouvoir - théoriquement - tenir 760 ans de veille (dans la pratique la pile se sera déchargée toute seule bien avant). En pratique on dit "c'est pas le courant de veille qui va devoir faire changer la pile !".
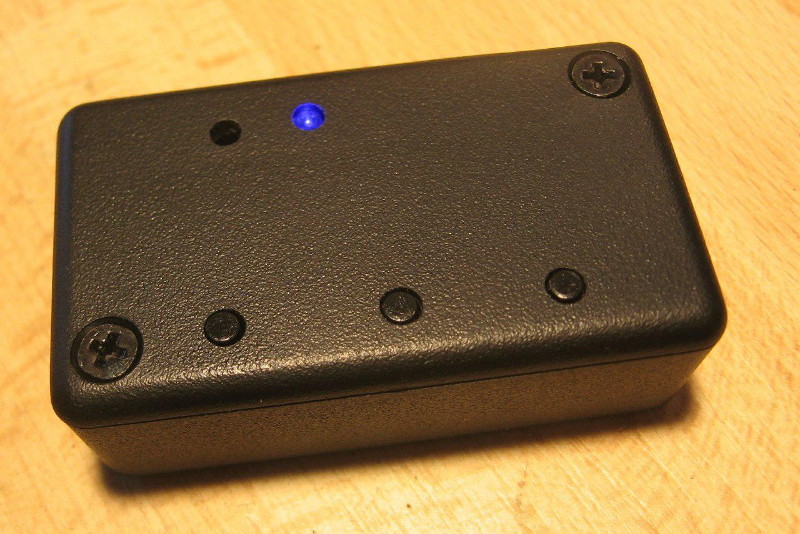
Le prototype...
... qui a du un peu passer à la fraiseuse pour qu'il puisse entrer dans le boîtier qui sera finalement choisi. Nota: trouver un moyen si possible simple pour monter les boutons un tout petit peu plus haut. J'en ai profité pour faire les trous dans le boîtier également à la fraiseuse, afin qu'ils soient correctement alignés, car si je perçais manuellement, je n'arriverai pas a être d'avantage précis qu'environ un demi-millimètre, ce qui ne serait pas très élégant sur un aussi petit boîtier. Ce prototype est expédié pour qu'ils puissent le tester (le matériel et le firmware) avant de valider la fabrication d'une petite série...
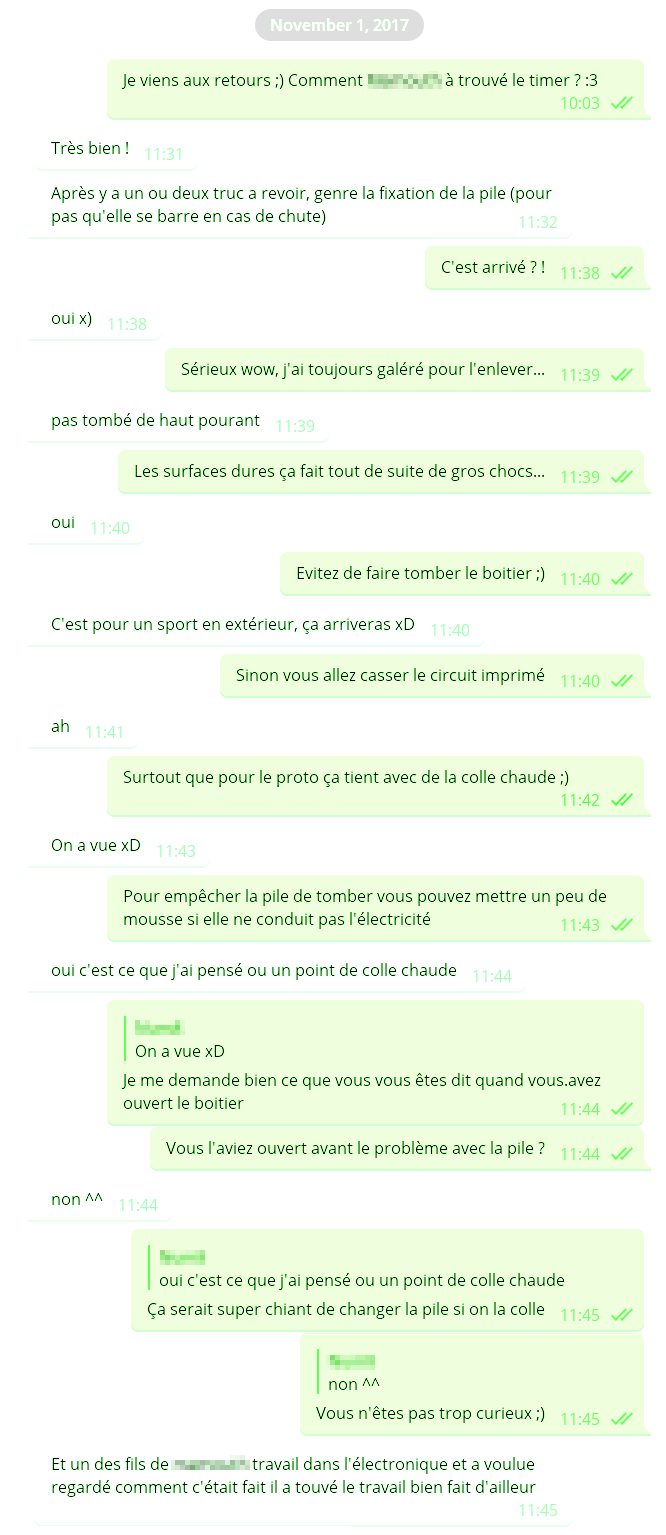
Nota, prévoir aussi tout de suite de la mousse pour caler la pile dans la version finale ^^'
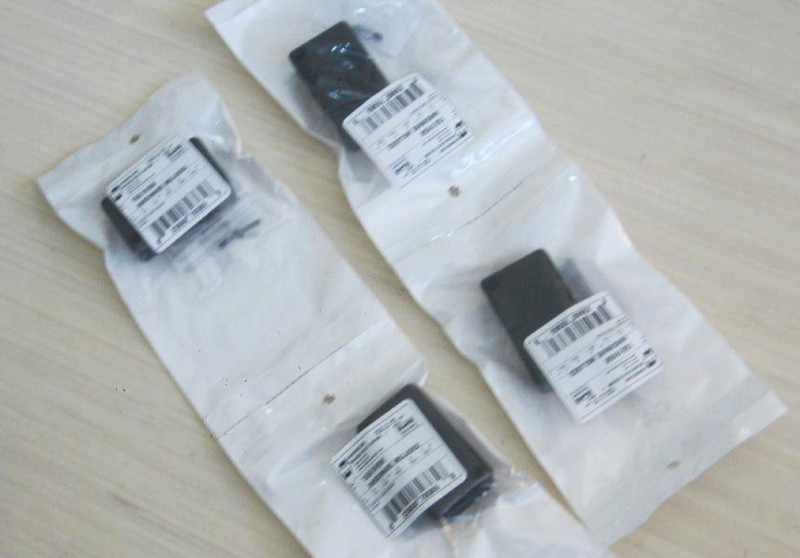
Passons aux choses sérieuses, commandons de nouveau quelques boîtiers...
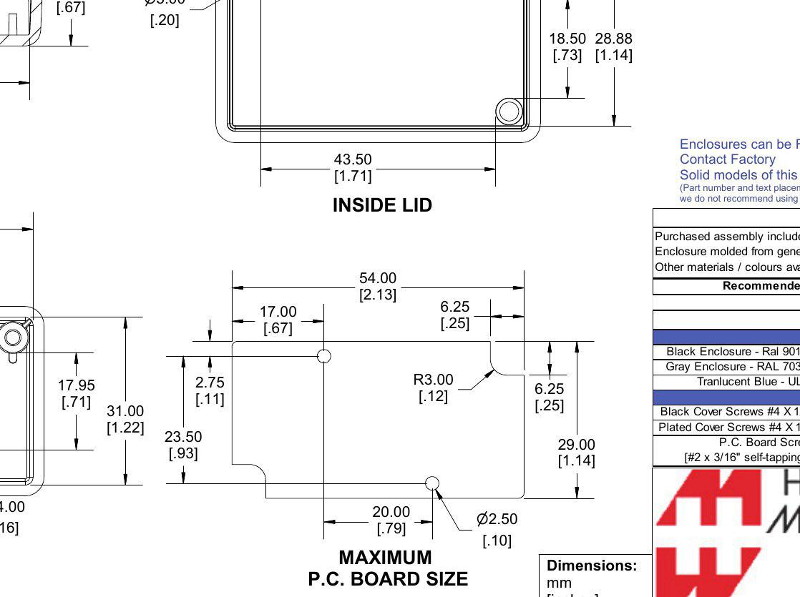
Le temps de concevoir le circuit imprimé final est venu, celui-ci devra rentrer sans soucis dans le boîtier...
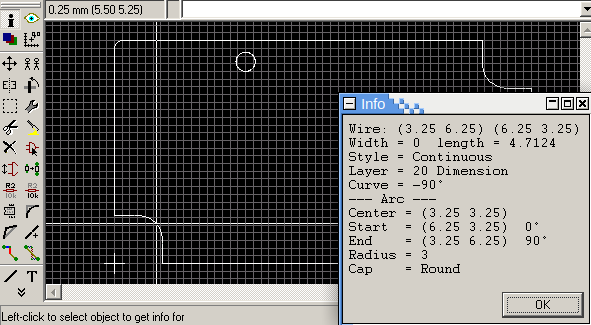
... alors forcément il faut recopier des cotes
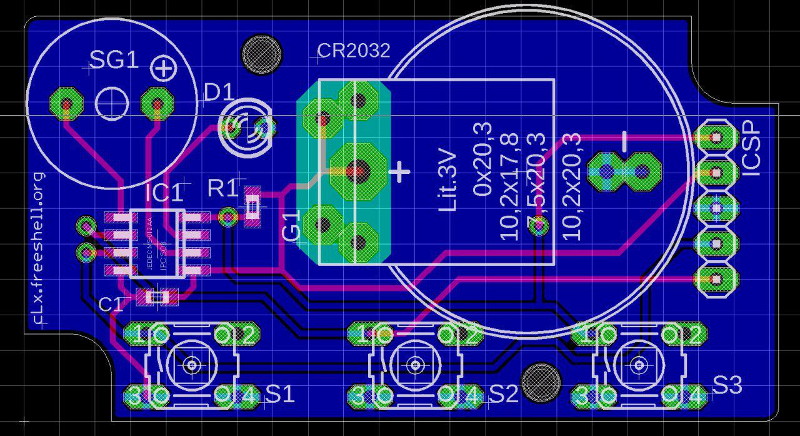
Suivi par le placement des composants et le routage des pistes. Faire attention à la place occupée par les têtes de vis !
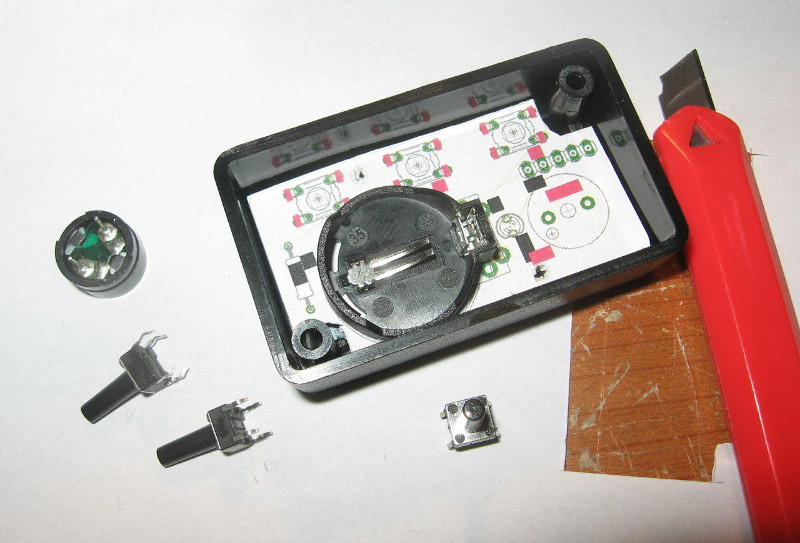
Astuce: Imprimer le board à l'échelle 1:1 sur du papier pour voir si tout se place correctement
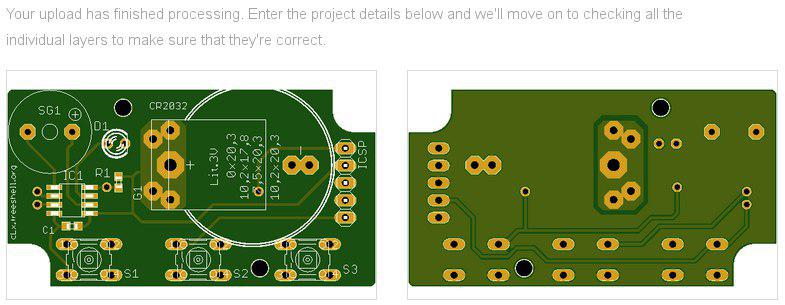
Sous-traitance du circuit imprimé, c'est le moment de ne pas laisser passer une éventuelle erreur...
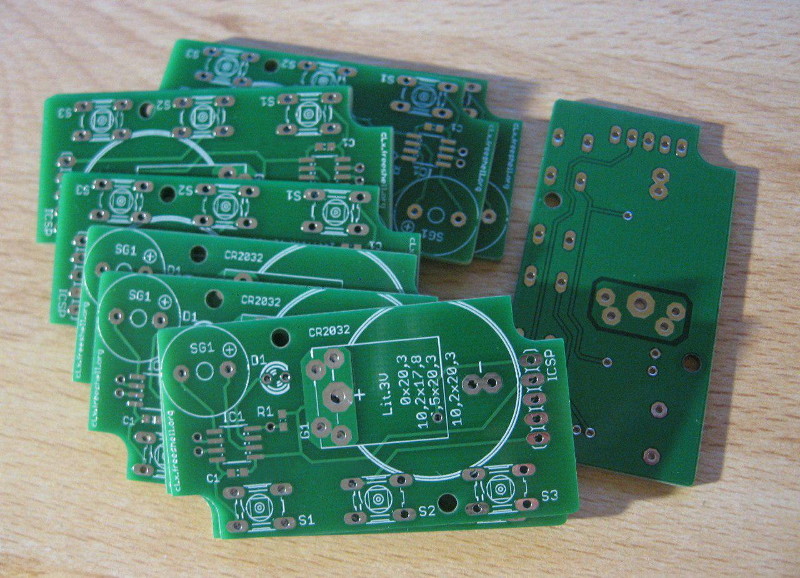
Les circuits imprimés sous-traités sont arrivés, alors, boulette or not boulette ?
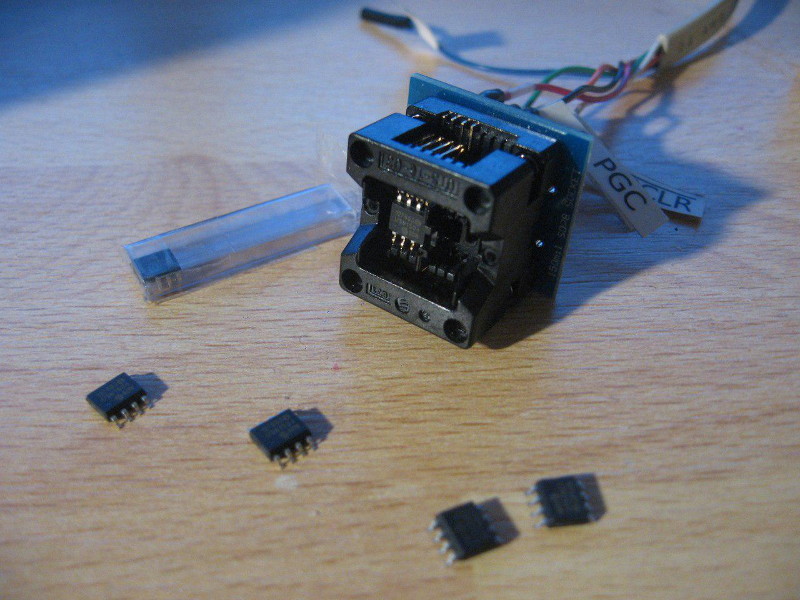
Comme j'ai pris les microcontroleurs sur eBay je trouve plus prudent de les tester avant de les souder ! Les supports ZIF pour CMS sont rigolos, aussi.
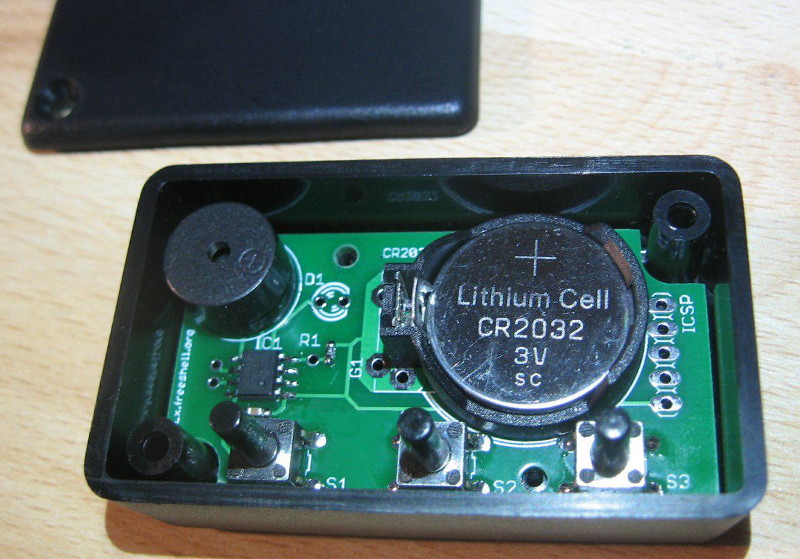
Circuit imprimé avec les composants tous soudés — sauf la LED, car comme aucun couvercle n'est encore percé, je n'ai pas encore déterminé la hauteur de montage de cette dernière, et il me manque aussi les vis de montage (non fournies avec les boîtiers, et la bonne dimension n'est pas précisée, donc il a fallu que je l'estime en mesurant les dimensions au pied à coulisse.
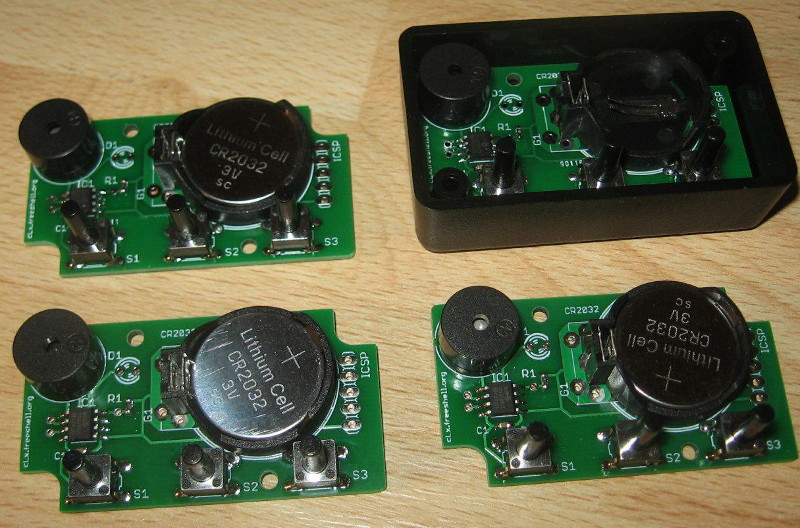
Soudage en série...
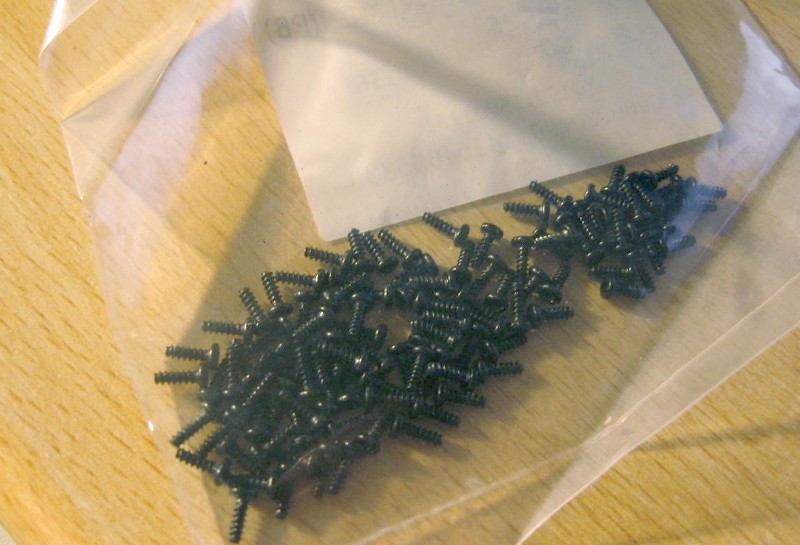
Les petites vis sont arrivées !

Les trous du circuit imprimés sont un petit poil larges mais pas de soucis à ce niveau là, c'est mieux ça que l'inverse, et le circuit se place correctement.
Maintenant il faut trouver une solution pour percer proprement les trous sur le couvercle du boîtier. Contrairement au prototype, je ne peux pas utiliser la CNC pour chaque couvercle, parce que ça demanderait trop de temps machine et trop de temps aligner et faire le zero... Ma solution est de faire un patron en aluminium permettant de guider le perçage manuel avec une perceuse à colonne.
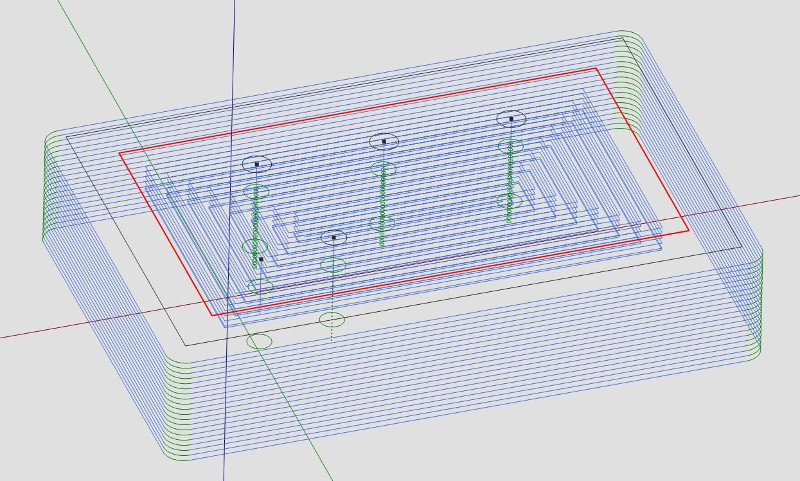
Préparation des fichiers GCode (déplacements machine), en reportant les dimensions du couvercle puis les coordonnées des boutons, de la led et du buzzer EN MIROIR, car dans le plastique le dessus du trou n'aura pas besoin d'ébavurage, ce qui sera plus propre
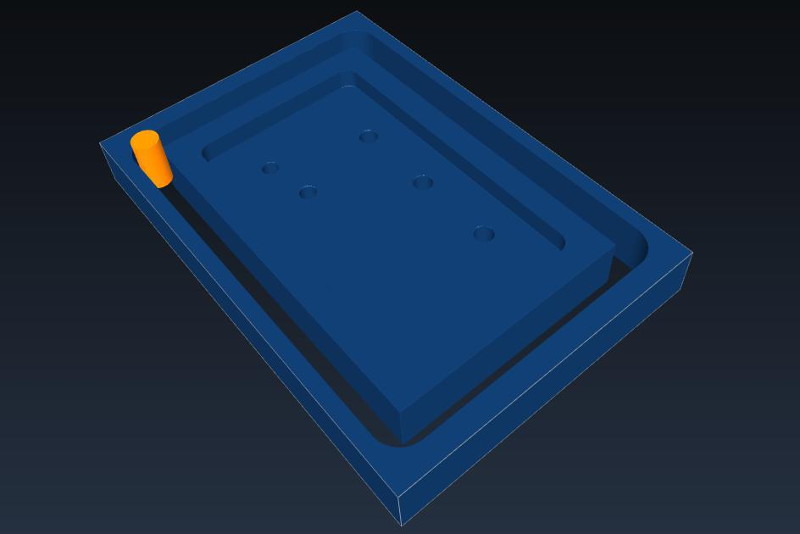
Simulation avec Camotics des fichiers GCode générés précédemment, en lui indiquant la dimensions des fraises que je vais utiliser à chaque étape
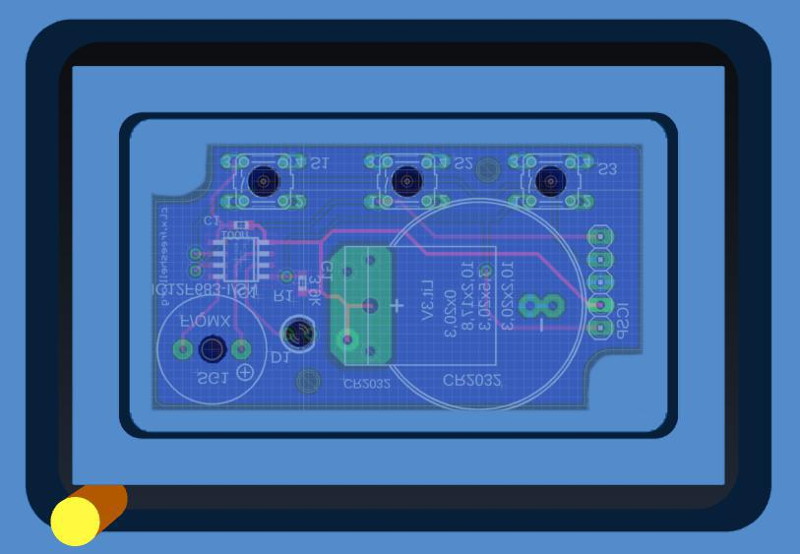
Superposition de captures d'écran en transparence pour se rassurer sur le bon alignement des trous
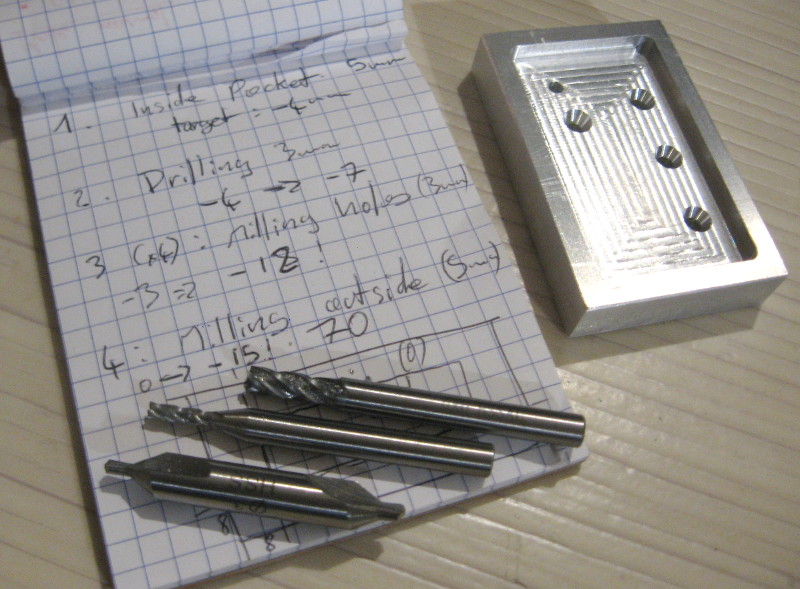
Mes notes, les outils utilisées, et le résultat. J'ai un peu merdé sur le zero en axe Z de l'étape de perçage, mais ce n'est pas gênant pour l'usage de cette pièce
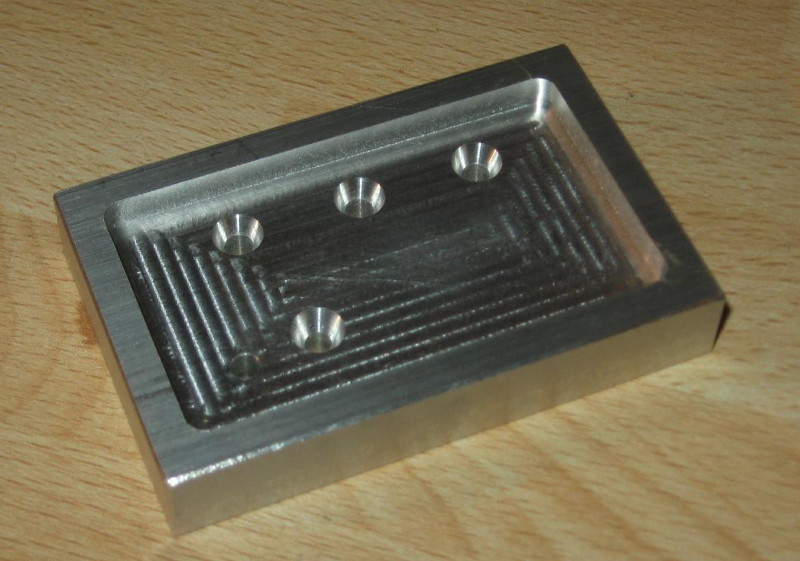
Template en gros plan.
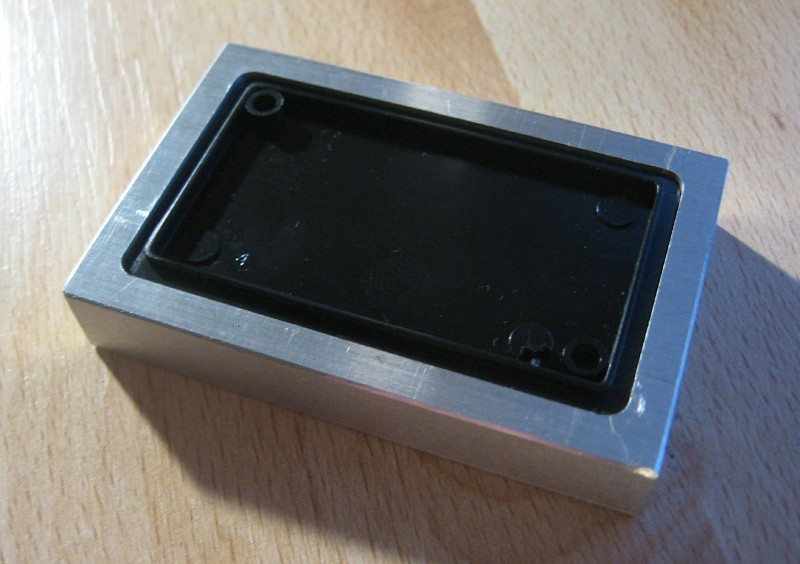
Les couvercles des boîtiers y entrent tout juste, comme il faut. Maintenant il suffit de retourner l'ensemble et de faire les trous (deux tailles de mèche différentes...)
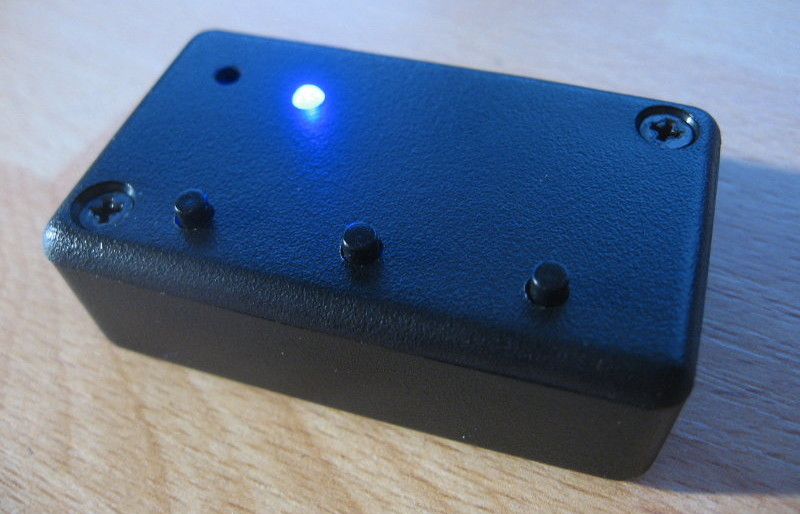
Résultat parfait, tout s'est bien passé. Il reste à faire la même chose avec les couvercles des autres boîtiers.
Vidéo Youtube montrant les différentes étapes de fabrication, et la vidéo "demo.mp4" de validation du prototype avant envoi par la poste de ce dernier
Anecdote rigolote : il me manquait encore deux boîtiers pour faire une série de dix unités complètes. Furrtek ayant eu la gentillesse de me proposer de les rajouter sur une commande chez un fournisseur et de passage, au retour d'une sortie Urbex, on a pu se faire une soirée pizza et le perçage des trous avec le template en aluminium s'est fait à l'arrache, par terre et à la visseuse, entre le moment où nous avons commandé les pizza et le moment où nous sommes allés les chercher. Tout ça la veille d'un voyage en train dans le sud-ouest au cours duquel j'en ai profité pour les remettre en main propre — après tout ce travail ça m'aurait fait mal que tous soient perdus par la poste !
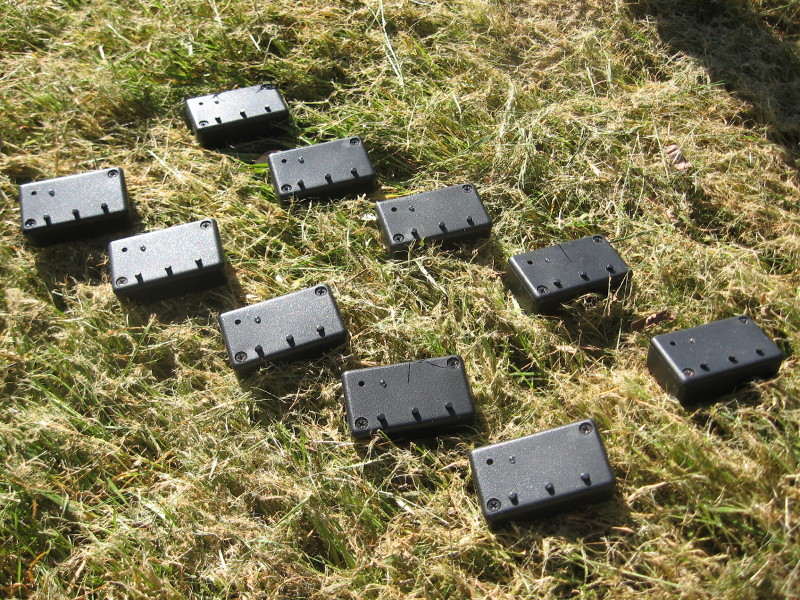
Une dernière petite photo en souvenir dans le sud-ouest !